FAQs
Using TempIT in Secure Applications
What is Mean Kinetic Temperature?
F0, A0 and PU Calculations
What is HACCP?
Using Signatrol Data Loggers in a Grow Tent
What is Validation?
What Is A Data Logger?
A data logger or datalogger is an electronic device that is used in conjunction with a computer to monitor or record various signals.
Remember when you were at school and you did experiments, measuring the temperature of boiling water, taking a reading every minute until it boiled. Well, a data logger would do this for you automatically. All you need to do is put the sensor in the water and tell the data logger how often to take a reading and at the end of the experiment, you download the information to the computer and it will produce a graph for you.
The data logger may have internal sensor(s) so it measures where it is located or it may have one or a number of channels where external sensors can be connected. Some data loggers can be configured to accept a wide range of sensors.
Using the computer, the data logger is programmed to "wake up" at predetermined intervals, take a reading and go back to sleep. The time period between readings is called the "sample period" and can range from many readings per second to once per day. The data logger will have an internal memory where the readings are stored. Once this memory is full, the data logger can be programmed to stop taking new readings, and therefore not loose any readings or, overwrite the oldest reading.
Once the data logger has been monitoring for the required time period, it is connected to the computer. The stored readings are then downloaded and saved on the computers hard disk. A graph can now be produced showing the measured signal over time - providing an accurate account of what the data logger measured - useful for proving a shipment got too hot in transit or that your office is too hot to work in!
Once the stored information has been downloaded from the data logger, the memory is cleared and the data logger is ready to be re-used over and over again - well, until the battery runs out, which is usually a number of years.
The majority of Signatrol's data loggers are battery powered and all have a battery life of at least 3 years.
Where Are Data Loggers Used?
Data loggers are used in a wide variety of applications from simple monitoring of temperature in an office environment to monitoring the temperature of perishable products in transit or optimising the production process of food, pharmaceutical or engineering products. The same data logger can be used in a variety of applications, if you want to make a record of temperature, humidity, pressure or Voltage and current signals, we have a data logger to suit your needs.
This is a typical graph that you would get from a Signatrol data logger. It was produced by our graphing software - TempIT ( pronounced "temp it") although some functions shown are only available in the PRO version:

What is response time?
Nothing responds in zero time and the response time is a measure of the time that a particular sensor takes to reach the equilibrium of the environment it is placed in. The response time can therefore be defined as the time required for a sensor output to change from its previous state to a final settled value within an acceptable tolerance band. Because sensors generally respond exponentially, they never actually reach their final value they just get closer and closer asymptotically until they are so close as to be regarded as settled. This can be an arbitrary value (say 99% of the change) or the point at which they are so close as to be within the tolerance of the sensor. This is further complicated because there are two generally accepted ways of stating response times i.e the 63% and the 10-90%. The 63% figure is called the time constant and is the time for the sensor to reach 63% of its final value. As a rule of thumb the sensor reaches 95% of its final value in 3 time constants and 99% in five time constants. The 10-90% is the time it takes for the sensor to traverse between 10% and 90% of its final value.
Call our sales office or submit an enquiry form for more details.

Using TempIT In Secure Applications.
TempIT can be used in FDA 21 CFR Part 11 applications if your procedures are written with TempIT in mind. Here we have a document that explains how each requirement can be accomplished.

TempIT File Locations.
For TempIT version 4.1.50 or later, the logger files are located in the Users, Documents Folder: C:\Users\******\Documents\Signatrol - TempIT replace ****** with your username.
For previous TempIT versions, see below.
The location of the logger files depends on the version if windows you are running.
For Windows XP the default location is: C:\Program Files\TempIT V4\Logger Files.
For Windows Vista, Windows 7 and Windows 8 (UAC on) the default location with be: C:\USERS\*******\AppData\Local\VirtualStore\Program Files\TempIT V4\Logger Files ******* replace with your username.
Each logger has a database file with the extension .sdb The serial number will make up part of the file name The database contains all graphs downloaded from the logger. You should rename your files if your customer is placing them in the same directory as his existing database files.
Also make sure you are running the latest version of TempIT
IATA 2017 Compatibility.
All SL50 series, SL151T and TempMate data loggers are exempt from the IATA 2017 regulations as they contain button lithium cells. All other data loggers may require declaration if they are flown on commercial or cargo aircraft.
Signatrol has an approved account for shipping Section II Lithium Metal and Lithium ION batteries by air.
SL50 Series Temperature Sensor.
The SL51T, SL52T, SL53T, SL54TH and SL55T-A have an internal temperature sensor that is silicon based. It is inside the die of a chip on a round printed circuit board in the middle of the can package.
The temperature sensor measures equally well in all directions.
What is Mean Kinetic Temperature?
It is widely recognised that calculating MKT gives a far more representative picture of the effect of temperature change on sensitive materials, such as pharmaceuticals and food products, during storage and distribution. The shelf life of sensitive materials is directly related to MKT.
Most Signatrol temperature data loggers, running TempIT-Pro software, can be configured to compute and record mean kinetic temperature (MKT).
The United States Pharmacopoeia (USP) defines MKT as a single calculated temperature at which the total amount of degradation over a particular period is equal to the sum of the individual degradations that would occur at various temperatures. In non-technical terms, MKT converts a variable temperature into an equivalent steady temperature, which is used to determine the effect of the excursion on product quality. For example, USP recommendations for “controlled room temperature” state that the temperature should be maintained between 15°C and 30°C, with a MKT of less than 25°C. The calculation gives increased weighting to higher temperature excursions than normal arithmetic methods, recognising the accelerated rate of thermal degradation of materials at higher temperatures.
Measuring MKT with Signatrol data loggers
The Signatrol SL151T temperature loggers are specifically designed to travel with goods and provide a detailed date and time temperature profile that can be used to highlight any problems. The data loggers are housed in a fully weld-sealed, crevice-free, food-grade polystyrene bags that are only 10mm thick. These data loggers are the only ones approved by the Royal Institute of Public Health.
The Signatrol SL151T data logger series uses a patented induction technique for set-up and data download. As a result, there are no plugs, sockets or entries of any kind, thereby avoiding potential “bug traps” and ensuring full sealing. Powered by an internal battery, these data loggers can log at intervals from 30 seconds to 100 hours and have a measurement range from -30°C to +60°C. They have a delayed start feature that allows them to function according to a specific travel schedule and have an internal capacity of 24,576 readings, which means they can keep recording for more than four years.
As well as the Signatrol SL151T series, the Signatrol TempMate2, SL52T and SL7000 data loggers can also be used to measure MKT
Calculating MKT with TempIT-PRO Software
If you use Signatrol TempIT-Pro software, you can quickly and assuredly calculate MKT. The software has an in-built calculator that carries out this task. TempIT software is free to download. MKT can be also calculated using the Arrhenius equation.
Using Signatrol TempIT-Pro software, all you have to do is enter the activation energy during set up (this can vary from 42-125 kJ/mol). The activation energy can be determined by differential scanning calorimetry.
MKT = (-DH/R)/Ln{(SUM(exp(-DH/R*Tn))))/n}
DH is the activation energy, R is the universal Gas Constant (.0083144 kJ/molK), T is the temperature in Deg K, and n is the total number of equal time periods over which data are collected. Ln is the natural log, exp is the natural log base and SUM is the total over n periods.
For more information about Signatrol data loggers and data logging systems, contact us on 01684 218528 or by using our enquiry form.
F0, A0 and PU Calculations
What is F0?
This is a brief introduction to the F0 Concept as applied to sterilisation. It is by nature brief and simplified. Customers are recommended to do their own additional research.
F0 is the sterilisation time to ensure that whatever micro-organisms are contained within the process sample are reduced to an acceptable limit. This is a function of both time and temperature and, historically, the sterilisation temperature has been 121.11°C (250°F). However in a real process, the temperature is never ideal and never exactly at 121.11°C. This would not be a problem except that the sterilisation time is extremely sensitive to temperature deviations e.g. 0.1 °C causes approximately a 2% change in the time required, 1°C causes a 24% change in time. It is possible , of course, to cater for worst case but this means that there is generally over sterilisation which, in the case of food, can result in a degradation of flavour and in any event more energy will be used than is necessary. F0 is a way of calculating the sterilisation time equivalence for temperatures other than 121.11°C. If the temperature is lower then the time needs to be extended and similarly, if it is higher that time may be shortened. The F0 calculation requires two parameters which can be entered in the Options>Configuration>graph screen. These are t0, the minimum temperature at which you start to sterilise (Default 90°C) and Z which is a constant determined by the micro-organism targeted and the ultimate Lethal Ratio which is deemed acceptable (Default 10).
How it is used?
Suppose that we are looking for a F0 of 12 minutes i.e. to obtain the required Final Lethal Ratio the sample needs to be held at 121.11°C for 12 minutes. A Signatrol data logger is used to plot the actual sterilisation cycle. With the graph on the screen, click on ‘Show Measure’ on the LHS. Two vertical bars appear that can be moved by clicking the cursor on them and then dragging. The start bar should be placed at the start of the cycle, the right hand bar can then be dragged across the graph and the F0 at the point of placement is shown in the table. As you can see F0 is in minutes and increased as the bar is dragged to the right until the temperature falls below 90°C and which no further sterilisation takes place. (Note the F0 value only updates
when the mouse click is released). When 12 Minutes is seen, the sample will have been sterilised to the required level. This can be considerably less time that waiting for the sample temperature to rise to 121.11°C and holding it there for 12 minutes and allowing it to cool, thus saving time and energy and hence costs.
What is A0?
A0 is exactly the same as F0 but in this case instead of the equivalent temperature being normalised to 121.11°C it is normalised to 80°C. This is used in lower temperature systems such as washer sterilisers etc.
And PU (Pasteurisation Units)
The same equation can be used to quantify the amount of micro-organism reduction during a pasteurisation process. Some products, especially dairy products, are heat treated at much lower temperatures to eliminate bacteria. The most common method is to use a process known as Pasteurisation (named after the method’s inventor, Louis Pasteur). The amount of pasteurisation (Time-Temperature) is quantified in Pasteurisation Units. One Pasteurisation Unit (PU) is defined as 1 minute of applied heat at 60°C. The number of PU’s required for a particular product depends a great deal on the product, specific bacteria, its packaging and anticipated shelf life etc.
The pasteurisation process starts at 50°C and therefore our defaults are start at 50°C calculate PU’s at 60°C with a Z=7 but all these parameters can be changed.
What is HACCP and how can Signatrol help with compliance?
HACCP - Hazard Analysis and Critical Control Point. HACCP is an internationally recognised system for reducing the risk of safety hazards in food.
A HACCP System requires that potential hazards are identified and controlled at specific points in the process. Plans are prepared for each process or product to identify possible hazards and controls are put in place to ensure that the hazards are eliminated or controlled to acceptable levels in the food product.
Why use HACCP?
Awareness of food-borne illness is increasing and concern and legislation throughout the industry is driving the use of HACCP and HACCP based certification programs. HACCP is internationally recognised and the steps below detail how to implement a HACCP system.
The HACCP Process
The following steps (although not exhaustive) should be followed:
-
Conduct a Hazard Analysis
The first step is to evaluate the processes and identify where hazards are likely to occur. After identifying the hazards these must then be evaluated and the degree of risk to the user determined. Once the hazard has been identified the critical control points are determined where processes are put into place to eliminate these potentially dangerous hazards. These are points where the hazard must be controlled or there could be a risk to the end user. -
Identify the Critical Control Points
The steps in your process where controls must be applied to prevent or eliminate the hazards that have been identified? These are your critical control points. For each critical control point the preventive measure will need to be identified detailing how the hazard might be prevented. -
Establish Specific Temperature, ph, time, procedures
Establish a maximum or minimum limit for temperature, time, pH, salt level, chlorine level etc that will effectively control the hazard. -
Establish Critical Limits
The next step is to establish criteria for each critical control point. The criteria that must be met to control the hazard at that point and if therer are any regulatory requirements. -
Establish Monitoring Procedures
What to measure and how it will be measured. -
Establish Corrective Actions
Establish what actions need to be taken if a critical limit is not met. The actions taken have two purposes, to control any nonconforming product resulting from the loss of control, and to identify the cause, eliminate it and prevent the situation from reoccurring. -
Establish Record Keeping Procedures
Determine what records are needed to show that the critical limits have been met, and the system is in control. Any regulatory requirements should be addressed here. -
Establish Verification Procedures
The HACCP plan must be validated to ensure it is effective in preventing the hazards identified.
How can Signatrol help with HACCP?
Signatrol manufacture temperature and humidity data loggers for a variety of applications and have a number of products that are specifically of interest in the transportation of temperature sensitive goods. The data loggers are designed to help companies comply with HACCP requirements, especially in the transportation of temperature sensitive goods.
We know from experience that the most critical point in the cold chain is the interface between the different stages of transport. For example we have identified potential problems with goods moved from a temperature controlled warehouse using refrigerated trucks to a supermarket that were left for several hours in the hot sun waiting to be loaded into the supermarket storage facility, dramatically reducing the shelf life. In another example, sensitive drugs in a refrigerated container were left on a dockland quayside for several days with the container un-plugged.
We at Signatrol, are convinced that the only way to ensure the integrity of a shipment is to send a data logger along with the goods, accompanying them for the entire shipment start to end.
Fortunately we have several loggers designed to do this function: Tempmate single use, SL50 series button loggers, SL150 series etc. These loggers are portable, accurate and provide an inviolate record for audit and regulatory purposes some with alarm feature to immediately indicate if a particular shipment has been out of limits.
For further information please contact us on 01684 218528 or email sales@signatrol.com.
Using Signatrol data loggers in a grow tent
The Signatrol miniature button data loggers can measure temperature and humidity inside a grow tent. The SL54TH temp and RH data logger have been used in grow tents, grow rooms and polytunnels to ensure the temperature and relative humidity are kept at the optimum levels. The SL54TH data loggers are wireless and once in place can be monitored via our TempIT software.
What is Validation?
Validation is a word we often see that is used differently across different sectors. In the medical & dental world, validation means the equipment being used in procedures is fit for purpose and is operating within specification.
Validation is performed by a third party company who then provides a calibration certificate that is UKAS traceable which is then retained by the customer as part of their records.
At Signatrol, we offer a UKAS 17025 traceable temperature and relative humidity (RH) calibration service. It is cost effective and can be turned around within 5 working days, where the data loggers are then returned with a UKAS traceable calibration certificate.
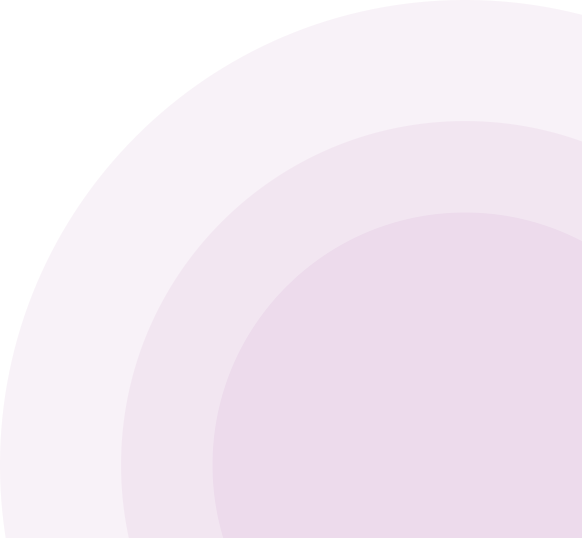